|
|
AC DEEP HOLE DRILLING |
|
What is Deep Hole Drilling |
|
The basic definition of deep hole drilling is to drill a hole multiple times deeper than the diameter of the hole itself. Holes of more than 100 times the diameter can sometimes be drilled.
Due to the growing demand for deep hole drilling in several industries AC Honed Group have acquired multiple deep hole drilling machines capable of handling different sizes, lengths and materials. AC Honed Group can drill holes of up to 1,1m diameter and up to 12 meters deep into various types of steels and materials.
There are various uses for deep hole drilling, for example: the make up of barrels from solid material or hollow bar, bearing, oil or cooling holes on rollers or rods, hollow shafts, hollow gear shafts, thick walled tubes etc. Short holes and blind holes can also be drilled with deep hole drilling machines. A blind hole is where the drill does not go all the way through the item, but only to a specific dept.
There are different types of deep hole drilling.
STS or Single Tube System:
Cutting fluid is supplied externally through the space between the drill tube and the drilled hole. The cutting fluid serves two purposes namely, to cool down the cutting tips and also to transport the chips through the inside of the drill tube towards the back of the drill tube where the chips are being separated from the fluid.
The Gundrill system:
Cutting fluid is supplied internally through the drill to the cutting edge. The gundrill has a V-groove on the outside to create space for the chips to pass through. The fluid forces the chips / shavings to the outside of the drill and out at the back. The gundrill does not have a detachable head, the head and drill is one piece.
The Ejector System:
The ejector system has an inner and outer tube. Cutting fluid is supplied through the space between the inner and outer tube towards the drill head. The drill head has several holes strategically placed to keep the cutting tips and pads cool. The chips / shavings are washed out through the inner tube towards the back.
There are also different methods of deep hole drilling.
Solid Drilling:
The process of drilling a hole through or into a solid piece of material. The straightness and surface finish tends to be very good with this type of drilling.
Counter boring:
When a part is drilled but there is already a smaller existing hole, its called counter boring. Counter boring is done when hollow bar or hollow material is used and the inside must be drilled larger or must have a machined finish. Also when machine power is not enough to remove all the material through solid drilling, a pilot hole is drilled and then material is removed bit by bit through counter boring.
Trepanning:
Trepanning heads are designed to leave a solid core in the middle of the hole behind. Instead of removing all the material from inside by cutting it to shavings it cuts out a circle around the center core. This method uses less machine power and in some instances saves time, but it is a very precarious process and the tooling is very expensive.
|
|
|
SPECIFICATIONS |
|
|
- From Ø 3mm to 1100mm, up to 12m long
|
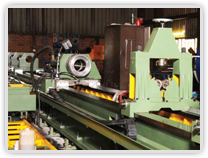 |
- Ø 300mm can be drilled straight from solid, up to 8m deep
|
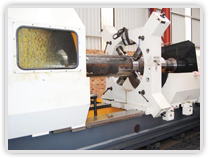 |
|
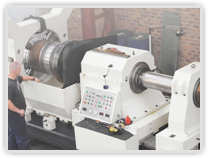 |
|
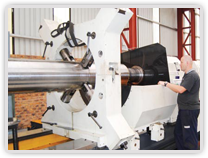 |
|
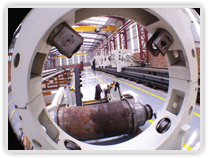 |
|
|
|
Deep Hole Drilling Machine at AC Honed Tube |
|
|
|
LEADING SINCE 1978 |
|